
Creating high-quality gravity die casting components involves a meticulous process with several critical parameters to ensure the final product meets the desired standards of strength, durability, and precision. Here’s an elaboration on each of the key parameters you’ve listed, incorporating technical data where applicable. This overview should provide a solid foundation for your blog and help share insightful content across social media platforms.

1. Pouring Velocity
Pouring velocity directly influences the formation of turbulence within the molten metal as it enters the mold, which can lead to air entrapment and subsequently, porosity. Optimal pouring velocities are crucial for minimizing these defects. For example, aluminum alloys might be poured at a velocity of around 0.5 to 1.0 m/s to balance between minimizing turbulence and ensuring complete mold filling. Excessive velocities can increase defect rates by up to 20–30%, depending on the complexity of the casting and the specific metal being cast.
The image illustrating the concept of pouring velocity in gravity die casting has been generated. It depicts the careful pouring of molten metal into a mold, emphasizing the controlled flow rate to minimize turbulence and ensure quality casting.

2. Melt Holding Time
The holding time for the molten metal before pouring affects the temperature uniformity and can lead to oxide formation if excessively long. Shorter holding times, typically less than 20 minutes for aluminum alloys, can reduce oxidation and associated defects by up to 15%. Oxidation not only compromises the mechanical properties but can also increase scrap rates due to inadequate casting integrity.
The image visualizing the concept of melt holding time in gravity die casting has been created. It highlights the critical process of maintaining the molten metal at a specific temperature within a furnace or crucible, ensuring the metal’s quality and uniformity are preserved before the pouring process.
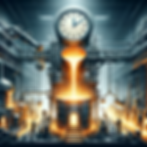
3. Pouring Time
Pouring time must be optimized to ensure complete mold filling without premature solidification. Insufficient pouring time can result in incomplete casting (misruns) or cold shuts, with defect rates potentially increasing by 10–20% for complex castings. The pouring time is closely related to the size and geometry of the casting, with larger castings requiring longer pour times.
The image depicting the process of pouring time in gravity die casting has been generated. It highlights the precision and timing required during the pouring phase to ensure complete mold filling without defects.

4. Mold Temperature at the Time of Pouring
The initial mold temperature can significantly affect the solidification rate and the final microstructure of the casting. Mold temperatures that are too low may increase the incidence of cold shuts and misruns by 15–25%, while excessively high temperatures can lead to longer solidification times and increased porosity. For aluminum casting, an optimal mold temperature range is between 200°C and 250°C.
The image illustrating the concept of mold temperature at the time of pouring in gravity die casting has been created. It emphasizes the importance of monitoring and achieving the optimal mold temperature before the pouring process to ensure the quality and success of the casting.
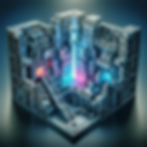
5. Gate and Riser Design
Proper gate and riser design can minimize the occurrence of shrinkage porosity by ensuring adequate feed metal is available as the casting solidifies. Poor gate and riser design can lead to increased scrap rates of 5–15% due to shrinkage defects. The design must consider the casting’s geometry, the thermal properties of the metal, and the solidification characteristics.
The image visualizing the concept of gate and riser design in gravity die casting has been generated. It provides a cross-sectional view of a die casting mold, showcasing the critical role of gate and riser systems in ensuring the molten metal flows correctly, fills the mold cavity efficiently, and solidifies with minimal defects.

6. Degasification
Effective degasification can reduce porosity levels by up to 20% in non-ferrous metal castings. The specific reduction in defect rate depends on the initial gas content of the melt and the efficiency of the degasification process. For aluminum alloys, using inert gas fluxing can decrease hydrogen levels to less than 0.1 mL/100 g Al, significantly improving casting quality.
The image illustrating the process of degasification in gravity die casting has been generated. It captures a foundry worker using degassing equipment to introduce inert gases into molten metal, a critical step to enhance the metal’s purity and minimize porosity in the final casting product.
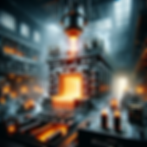
7. Preheat Temperature
Mold preheat temperature affects the metal’s fluidity and the rate of solidification, impacting the casting’s mechanical properties and surface quality. Incorrect preheat temperatures can lead to thermal mismatches, increasing defect rates by 10–20%, particularly for thermal cracking and distortion.
The image showcasing the process of preheating a mold for gravity die casting has been generated. It captures the critical preparation step, emphasizing the use of heating methods to bring the mold to the optimal temperature, ensuring a successful casting process.

8. Die Coat Material and Thickness
The choice and application of die coat directly influence the surface quality and lifespan of the mold. Inadequate die coat can lead to sticking, increased wear on the mold, and surface defects on the casting. Optimizing the die coat can improve the release of the casting from the mold and reduce surface defects by up to 30%.
The image illustrating the application of die coat material on a gravity die casting mold has been created. It shows the detailed process of applying a uniform layer of die coat, emphasizing the precision required to ensure the quality of the casting surface and the longevity of the mold.
Each of these parameters plays a vital role in determining the quality and success of gravity die castings. By meticulously controlling these aspects, manufacturers can produce high-quality castings with the desired properties and minimal defects. Your blog can serve as an informative resource by detailing these technical aspects, thus helping readers understand the complexities and precision required in the gravity die casting process.
— GG — FF